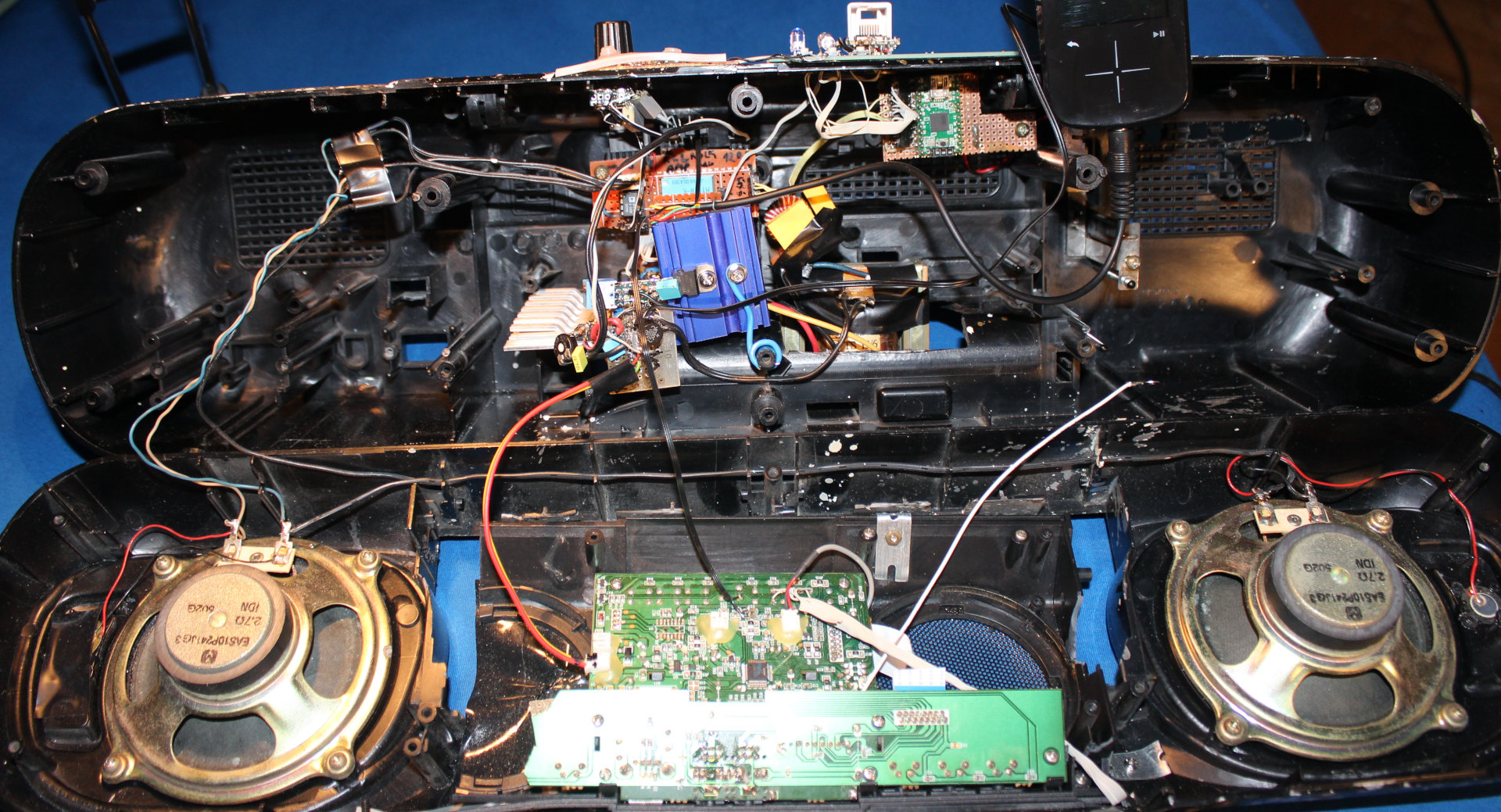
⏱️Overview
This is a continuation of my previous kitchen HiFi modding. Now with replaced electronics for power supply, amplifier and input selectors. Only radio and case stayed the same. So roughly half is made by me.
✍️Motivation
Previously there was here an ancient old power amp chip LA4108, from around 1995 or so when this HiFi was build, with 2 cassette decks. This amp was way too powerful and not quality enough for our times. Since I didn’t need much power, I just remade it with a very simple op amp amplifier, feeding speakers. I also wanted a holder to put my old audio player in place instead of just lying flat and hardly seeing its LCD. Lastly my mother found it hard to see what to press for radio and lost the volume knob behind our kitchen stuff since I moved it on side.
📊Features
- Op-amp amplifier feeding 2.7 Ω speakers through 47 Ω resistors. I still had OP275 lying around since like 2002 so I used it. Well it could be NE5532 or anything really. I didn’t bother with any transistors (class AB or A) at all to boost current or more power op-amps, because it was enough and we don’t need to hear it too loud 🔉🤫.
- Selecting 1 of 3 audio inputs from: FM radio, player (Sansa Fuze+ with Rockbox firmware), and external audio cable (going from my room to kitchen, analog but through Ethernet cable).
This is done using a MCU (worst for today Teensy 2.0, only because I have bought it long ago when I started and wanted to use it for any purpose finally, it’s ancient 8bit and 5V too, while I moved to 3.3V in my keyboards and all). Code was like just 50 lines, 3 buttons, 2 outputs for old 12V stereo relays, and 3 outputs for LEDs to show which input is selected to play. - Power supply for player 4.1V not from battery anymore, slightly with noise due to this.
Op amp uses +-16 V from 2 regulators LM317 and LM337 from a 15W transformer (could be less, but it’s what I got since years waiting, not used). Another with 12V for relays, and 5V for MCU. So yeah kind of nuts 5 voltage regulators here. It’s likely the reason it takes 3.5W from 220V wall, already doing nothing and about 5W doing something.
⌛Conclusions
Well half of my conclusions are already in my previous project for this HiFi back there. I.e. no reason at all to buy new stuff, better to modify this over 20 year old classic, especially after I painted it so funny. It was also working so best to extend it further and make it better for me.
So far I can say it is a joy to use and really good audio quality for me. I didn’t hear any noise, especially not like before. I hope it will last for few years at least, until I come up with something new I’d like to add. Or possibly get my stuff from inside and use new speakers, who knows.
One definite down side is that it took me about 5 days of holiday to do this, so it was way more than I’d like and lots of work still.
Another bad thing is that it uses 4 W power constantly, likely just because of so many voltage regulators here. But I won’t complain about this. I got more power lost in stuff that’s constantly on in the house all the time.